Revealing the Intricacies of Bolts and Machining Processes for Optimal Performance
In the realm of design and manufacturing, the choice of bolts and the intricacies of machining processes play a critical duty in figuring out the supreme efficiency and longevity of an item. From the relatively straightforward job of choosing the appropriate type of fastener to the facility precision machining strategies used, every action in this process needs careful focus to information. As we start this exploration right into the globe of bolts and machining, we will certainly reveal the subtle yet crucial elements that can significantly influence the efficiency and top quality of the last product, clarifying the typically ignored elements that can make all the difference in achieving ideal efficiency.

Relevance of Correct Bolt Choice
Choosing the suitable bolts is critical in making certain the architectural integrity and durability of any type of mechanical assembly. Bolts play an essential role in holding parts with each other securely, with the appropriate option contributing considerably to the overall efficiency and dependability of the assembly. When picking fasteners, factors such as product compatibility, environmental problems, load-bearing capability, and ease of setup should be thoroughly taken into consideration to guarantee optimum performance.
Inappropriate fastener option can cause a series of issues, consisting of loosening, rust, and even structural failing. Utilizing bolts that are not suited to the details requirements of the setting up can compromise its capability and present safety dangers. For that reason, designers and designers must thoroughly review the application needs and choose fasteners that satisfy or go beyond the required requirements and requirements.
Additionally, the proper bolt selection process includes analyzing the joint layout, anticipated loads, vibration degrees, and possible thermal development or contraction to ensure that the selected fasteners can stand up to the operating problems properly. By prioritizing appropriate bolt option, suppliers can boost the top quality, resilience, and performance of their mechanical assemblies.
Types and Qualities of Fasteners
An essential facet of mechanical assemblies depends on comprehending the varied kinds and special attributes of bolts made use of in various commercial applications. Bolts are important elements that hold structures together, guaranteeing stability and functionality. There is a variety of fasteners readily available, each made for details objectives based upon the application demands. Common sorts of bolts consist of screws, bolts, nuts, pins, washers, and rivets.
Screws are threaded fasteners that are commonly made use of to sign up with two or even more elements together. Screws resemble screws yet are usually used with a nut to develop a protected joint. Nuts are inside threaded fasteners that mate with bolts to hold parts together. Washing machines are thin plates that disperse the load of a bolt, avoiding damages to the material being attached. Rivets are long-term bolts that are hammered or pressed right into location. Pins are made use of for positioning or to safeguard elements momentarily.
Recognizing the features of each kind of bolt is crucial for picking the right one for a particular application, ensuring optimum efficiency and integrity of the mechanical setting up. Fasteners and Machining.
Accuracy Machining Strategies for Performance
The complex style demands of various fasteners demand using precision machining methods for optimal performance in producing procedures. Precision machining is essential in ensuring that bolts satisfy the precise specifications required for their designated application. One of the key strategies utilized in precision machining is Computer system Numerical Control (CNC) machining, which makes it possible for high degrees of accuracy and repeatability in the manufacturing of fasteners. CNC machines can doing complex cuts and forming operations with minimal human treatment, resulting in boosted efficiency and uniformity in the manufacturing procedure.
Along with CNC machining, other precision strategies such as grinding, milling, and transforming are frequently made use of to Click This Link attain the tight tolerances required for bolts. These methods enable suppliers to develop fasteners with smooth surface areas, precise measurements, and high structural integrity. By using accuracy machining techniques, makers can boost the quality of fasteners, lower material waste, and enhance general manufacturing efficiency. The usage of innovative machining procedures helps guarantee that fasteners satisfy market criteria and consumer expectations for efficiency and dependability.

Elements Affecting Machining Process Performance
Numerous variables play a considerable duty in figuring out the efficiency of machining processes in the production of fasteners. The very first vital factor is the option of reducing devices. Selecting the proper devices based on the material being machined, wanted finish, and cutting speeds can substantially impact the efficiency and quality of the machining process. In addition, the cutting parameters such as cutting rate, feed price, and depth of cut are necessary variables that affect performance. Fasteners and Machining. Optimizing these specifications based upon the details requirements of the bolt being generated is essential to accomplishing specific and cost-effective machining.
Equipment rigidness and stability additionally play a crucial duty in identifying machining process efficiency. An educated operator can make real-time adjustments, troubleshoot concerns efficiently, and ensure that the machining procedure runs smoothly, inevitably impacting the last high quality of the fastener.
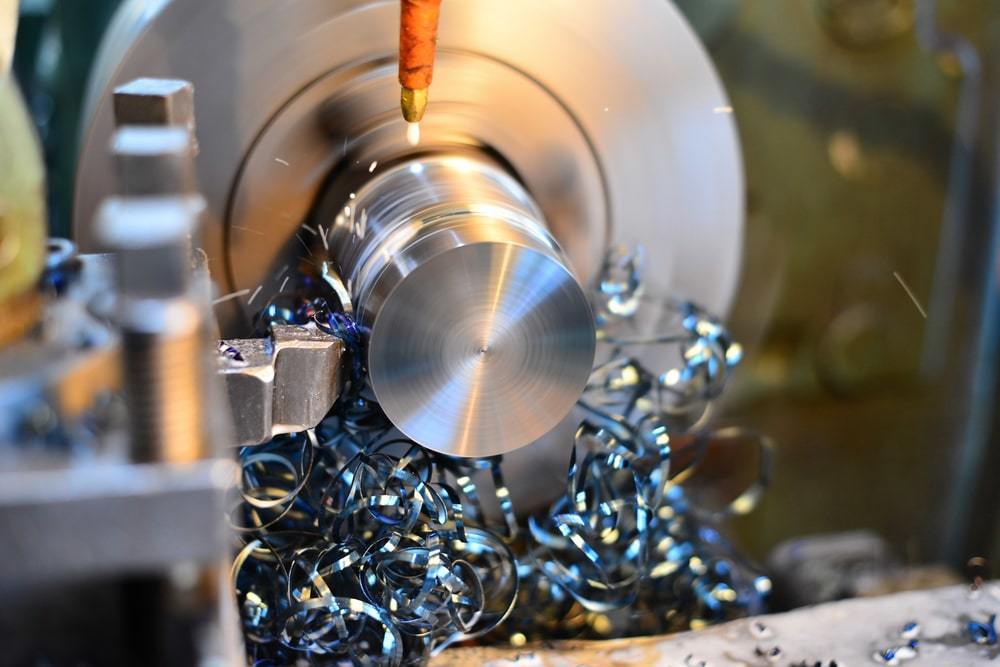
Quality Assurance Steps in Manufacturing
Elements affecting machining process performance, such as reducing device selection and equipment stability, directly influence the implementation of high quality control procedures in manufacturing. Normal maintenance of machining devices is additionally vital to support high quality control. By sticking to stringent quality control procedures, suppliers can enhance client contentment, build an online reputation for reliability, and inevitably attain ideal efficiency in their machining procedures.
Final Thought
Finally, choosing the appropriate fasteners and utilizing precision machining techniques are essential for ideal performance in making processes. Comprehending the types and characteristics of fasteners, in addition to aspects this content influencing machining process efficiency, can cause enhanced effectiveness and high quality control actions. By taking notice of these details, suppliers can accomplish greater degrees of performance and reliability in their products.
In the realm of Discover More design and production, the selection of bolts and the ins and outs of machining processes play a pivotal role in figuring out the utmost performance and toughness of a product (Fasteners and Machining). One of the primary techniques used in accuracy machining is Computer Numerical Control (CNC) machining, which allows high degrees of precision and repeatability in the manufacturing of fasteners. The usage of advanced machining processes helps guarantee that bolts meet industry criteria and customer assumptions for performance and reliability
In conclusion, picking the appropriate bolts and making use of accuracy machining strategies are necessary for optimal performance in manufacturing procedures. Comprehending the types and attributes of bolts, along with elements influencing machining procedure efficiency, can lead to enhanced effectiveness and quality control steps.